ケミカルリサイクルが未来を変える!プラスチック廃棄問題解決への挑戦
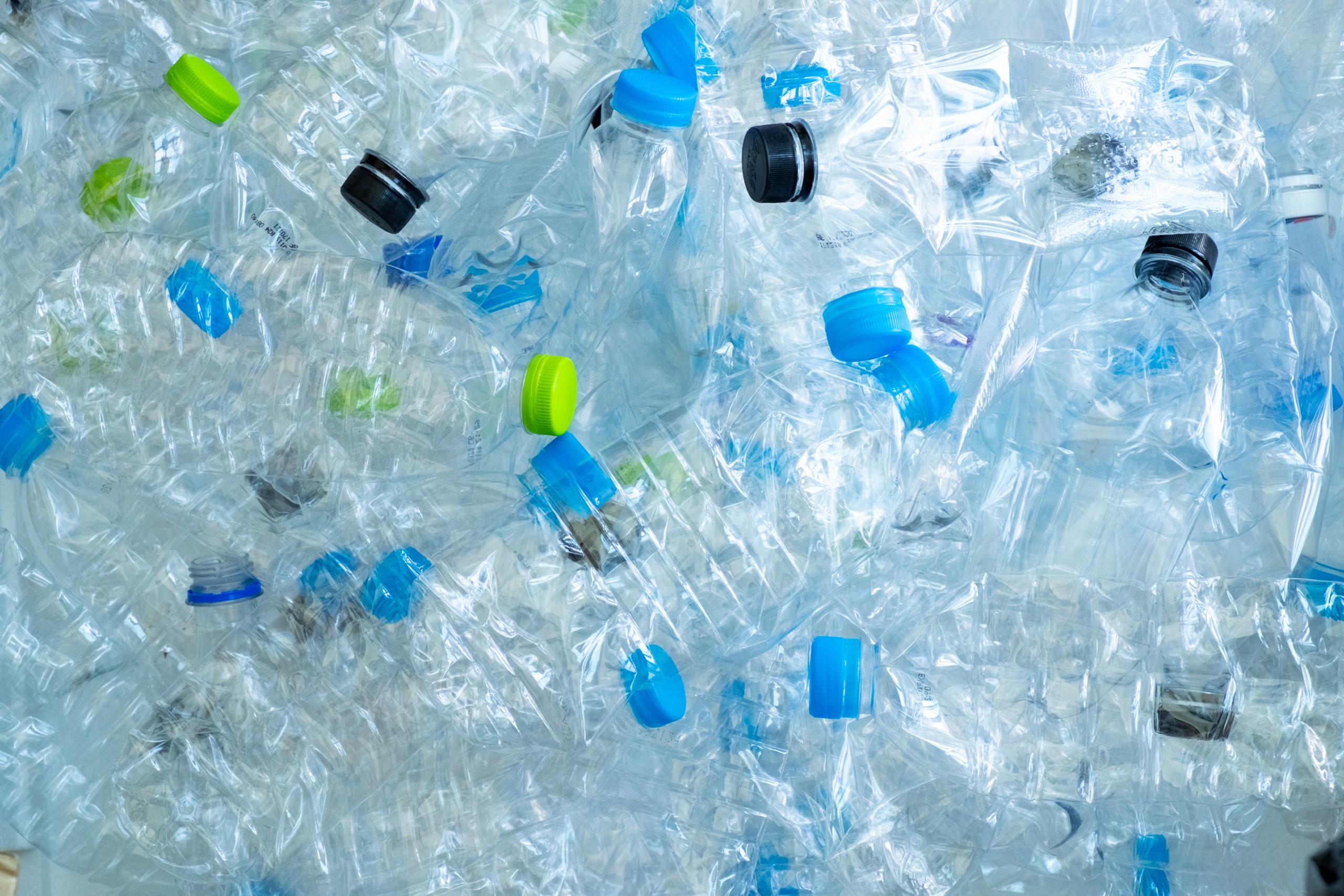
深刻化する廃プラスチック問題に、革新的なソリューションとして注目を集めているケミカルリサイクル。
従来のマテリアルリサイクルでは対応が難しかった混合プラスチックや劣化プラスチックを、化学的に分解して新たな資源として生まれ変わらせる技術です。
本コンテンツでは、ケミカルリサイクルの基本から最新動向まで、環境問題の解決に向けて押さえておくべきポイントを解説します。
マテリアルリサイクルとの違い、具体的な処理プロセス、そして導入における課題とメリット・デメリットを徹底的に分析。
さらに、先進企業の取り組み事例や自治体との連携モデルなど、実践的な知見もご紹介。
プラスチック資源循環の新たなステージを切り開くケミカルリサイクル。その可能性と実務での活用方法を、分かりやすく解説していきます。
目次
循環型社会を実現する「ケミカルリサイクル」とは
ケミカルリサイクルは、使用済みプラスチックを化学的に分解して、新しい製品の原料として再利用する革新的なリサイクル方法です。
従来の物理的な再生処理とは異なり、プラスチックを分子レベルまで分解することで、より高品質な再生材料を生み出すことができます。
この技術により、これまでリサイクルが困難だった複合素材や着色プラスチックも、効率的に再資源化することが可能になりました。
世界的な環境意識の高まりとプラスチック規制の強化に伴い、ケミカルリサイクルは循環型社会実現への重要な解決策として注目を集めています。
ケミカルリサイクルの基礎知識
資源の循環利用に役立つケミカルリサイクル。「マテリアルリサイクル」「サーマルリサイクル」「モノマーリサイクル」と、いろいろあり、難しく感じている方もいらっしゃるでしょう。
ここでは、そんなケミカルリサイクルについてわかりやすく解説していきます。
マテリアルリサイクルとの違い
マテリアルリサイクルとケミカルリサイクルには、以下のような明確な違いがあります。
- マテリアルリサイクル
- プラスチックを物理的に粉砕・溶融して再生
- 品質の劣化が避けられない
- 分別が厳密に必要
- 処理コストが比較的低い
- ケミカルリサイクル
- 化学反応で分子レベルまで分解
- バージン材料と同等の品質を実現
- 混合プラスチックも処理可能
- 処理コストは比較的高い
マテリアルリサイクルでは混合プラスチックや汚染された素材の処理が難しいのに対し、ケミカルリサイクルはこれらにも対応できるなど、さまざまな違いがあります。
サーマルリサイクルとは
サーマルリサイクルは、プラスチックごみを焼却して得られる熱エネルギーを利用する方法です。
この方式は、エネルギー回収という観点ではメリットがありますが、CO2排出や有害物質の発生という環境負荷が課題となっています。
また、プラスチック自体が失われてしまうため、資源の再利用という観点では課題が。資源の循環利用という観点では、マテリアルリサイクルやケミカルリサイクルの方が望ましいとされています。
モノマーリサイクルとは
モノマーリサイクルは、ケミカルリサイクルの一種で、プラスチックを元の単量体(モノマー)まで分解して再利用する方法です。
この技術は、特にPETボトルやナイロンなどの縮合系ポリマーに対して効果的です。
分解して得られたモノマーは、新しい製品の原料として何度でも使用することができ、品質の低下もほとんどありません。
最新の研究では、より効率的な触媒や分解方法の開発が進められており、処理コストの低減も期待されているのです。
企業が注目するケミカルリサイクル導入のメリット
企業の環境戦略において、ケミカルリサイクルの導入は大きな競争優位性をもたらします。
従来のリサイクル手法では対応できなかった課題を解決し、環境負荷の低減とビジネス成長の両立を実現できるでしょう。
以下では、具体的なメリットについて詳しく解説していきます。
難処理プラスチックへの対応が可能
ケミカルリサイクルの最大の特徴は、これまでリサイクルが困難だった素材も処理できる点です。
複合材料や着色プラスチック、汚れの付着した包装材なども、分子レベルまで分解することで再資源化が可能になります。
たとえば、自動車部品メーカーでは、様々な素材が混在する部品でも一括処理できるようになり、リサイクル率が大幅に向上。
今後は処理技術の進歩により、さらに多様な素材への対応が期待されています。
品質の高いリサイクル材を生成
ケミカルリサイクルで生成される再生材料は、バージン材料と同等の品質を実現できます。
化学的な分解・精製プロセスにより、不純物や劣化成分を除去し、高純度な原料として再生することができます。
食品包装メーカーでは、この特徴を活かして食品グレードの再生プラスチック製造に成功しており、新たな市場を開拓。
品質面での信頼性が高いため、高付加価値製品への活用も進んでいます。
廃棄物削減と環境負荷を軽減
ケミカルリサイクルの導入により、埋立処分量とCO2排出量の大幅な削減が可能です。
従来は焼却処分されていた廃プラスチックを資源として循環させることで、環境負荷を最小限に抑えることができます。
環境規制の強化に対応しながら、持続可能な事業運営を実現できるでしょう。
持続可能なブランドイメージを向上
ケミカルリサイクルへの取り組みは、企業の環境配慮姿勢を効果的にアピールできます。
消費者の環境意識が高まるなか、リサイクルへの積極的な投資は、ブランド価値の向上につながるでしょう。
化粧品業界では再生プラスチックを使用した容器をアピールポイントとし、環境に配慮した商品として高い評価を得ています。
サステナビリティレポートなどを通じて、具体的な取り組みを発信することで、企業価値の向上が期待できます。
ケミカルリサイクル導入のデメリットや課題をチェック
ケミカルリサイクルには多くのメリットがある一方で、実用化に向けてはいくつかの課題も存在します。
これらの課題を事前に理解し、適切な対策を講じることが、成功への重要なポイントとなります。
以下では、主要な課題とその対応策について、具体的に解説していきます。
コスト
ケミカルリサイクルの導入には、従来の処理方法と比べて高額な初期投資が必要です。
▼主なコスト要因
- プラント設備の建設費用
- 運転・メンテナンス費用
- エネルギー消費コスト
- 専門技術者の人件費
しかし、規模の経済性や技術革新により、徐々にコストは低減傾向にあります。
政府の補助金制度や環境投資減税の活用で、初期負担を軽減することも可能です。
処理技術
現状の処理技術には、まだいくつかの技術的な課題が残されています。
特に、異物の混入や素材の品質のばらつきが、安定的な処理の妨げとなることも。
そのため、研究機関や企業の技術開発部門では、問題改善のための取り組みが行われています。
▼重点開発項目
- 分解効率の向上
- 不純物除去技術の確立
- エネルギー効率の改善
- 処理能力の向上
これらの技術課題は、産学連携による研究開発の進展で、着実に解決に向かっています。
安定的な原料確保
リサイクル事業の継続には、安定的な廃プラスチックの確保が不可欠です。
現状では、回収ルートの整備や分別収集システムが十分に確立されていない地域も多く存在します。
この課題に対しては、以下のような取り組みが進められています:
▼原料確保への対策
- 自治体との連携強化
- 収集業者とのネットワーク構築
- 企業間での回収システム共有
- デジタル技術を活用した効率的な回収
特に、複数の企業や自治体が連携したコンソーシアム方式での取り組みが、効果的な解決策として注目されています。
ケミカルリサイクルの実践的な導入事例と成功のポイント
世界中の先進企業が、ケミカルリサイクルの実用化に向けて革新的なプロジェクトを展開しています。
サステナブルな循環型社会の実現に向けて行われている導入事例と、成功のポイントについて見ていきましょう。
BASF(ドイツ):ChemCycling™ プロジェクト
BASFは、熱分解技術を活用した革新的なケミカルリサイクルプロジェクトを展開しています。
混合プラスチック廃棄物から高品質な再生原料を生産し、自動車部品や食品包装材に活用。
2025年までに年間25万トンの再生原料生産を目指し、設備投資を加速させています。
欧州全域でパートナーシップを構築し、回収から製品化までの一貫したバリューチェーンを確立しています。
Dow(アメリカ):Advanced Recycling プロジェクト
Dowは、先進的な分解技術を用いて、複合材料のリサイクルに成功しており、特に食品包装材や建材など、高品質な再生材料の需要が高い分野に注力しています。
2030年までに100万トンの再生・再利用可能な包装材を提供するのが目標。
技術開発とインフラ整備の両面で、積極的な投資を継続しています。
JGCホールディングス(日本):プラスチック分解プロジェクト
JGCホールディングスは、独自の触媒技術を活用した効率的な分解プロセスを開発しています。
従来比30%のコスト削減を実現し、商業化に向けた実証実験を進めています。
2024年には年間処理能力2万トンの実証プラントが稼働予定。
地域自治体との連携により、安定的な原料調達システムを構築しています。
イオン(日本):廃プラスチックからのリサイクル事業
イオンは、店舗で回収した廃プラスチックを活用した循環型リサイクルを展開しています。
食品トレーや買い物かごなど、店舗で使用する製品への再利用を実現。
年間1万トン以上の廃プラスチックを回収し、約60%の再資源化率を達成しています。
消費者への環境教育も含めた総合的なアプローチを実施しています。
東レ(日本):繊維リサイクル
東レは、使用済みポリエステル製品を化学分解し、高品質な繊維として再生する技術を確立。
バージン材料と同等の品質を維持しながら、製造時のCO2排出量を50%削減しています。
2025年までに年間処理能力を5万トンまで拡大する計画です。
また、アパレルメーカーとの協業により、サステナブルファッションの実現にも貢献しています。
成功のポイント
1. 規模に応じたコスト最適化
設備投資とランニングコストのバランスを考慮し、段階的な規模拡大を計画することが重要。
初期は小規模実証から始め、市場ニーズに応じて段階的に設備を拡充していくアプローチが効果的です。
2. 技術パートナーシップの構築
単独での技術開発には限界があり、専門企業や研究機関との連携が不可欠です。
専門的な技術を持つパートナーと連携することで、プロジェクトの実現可能性が高まります。
3. 政策支援と規制遵守
各国・地域の環境規制や支援制度を把握し、最適な事業スキームを構築します。
補助金や税制優遇を活用しながら、コンプライアンスを確実に維持することが重要です。
4. リサイクルの収集・供給ネットワークの整備
安定的な原料調達のために、効率的な回収システムの構築が必要です。
自治体や小売業者との連携により、持続可能な収集ネットワークを確立します。
5. 消費者認知と市場需要の喚起
消費者の意識を高める活動や、需要を喚起するマーケティングが成功の鍵となります。
環境教育や情報発信を通じて、リサイクル製品の付加価値を訴求することが大切でしょう。
6. ライフサイクル全体での環境負荷軽減
製品設計から廃棄までの全工程で、環境負荷を最小化する取り組みが必要です。
エネルギー効率の改善や再生可能エネルギーの活用により、総合的な環境性能を向上させます。
ケミカルリサイクルの課題解決への具体的アプローチ
ケミカルリサイクルの実用化に向けた課題を、具体的な解決策とともに解説。
各企業の成功事例や最新の技術動向を踏まえて、実践的なアプローチを提案していきます。
現状の処理コスト削減方法
ケミカルリサイクルの普及には、処理コストを抑える取り組みが重要です。
設備の最適化 | ・AIによる運転制御の導入 ・設備稼働率の向上 ・メンテナンス費用の低減 |
エネルギー効率の改善 | ・排熱回収システムの導入 ・再生可能エネルギーの活用 ・断熱性能の向上 |
原料調達の効率化 | ・地域内での回収網整備 ・異物混入率の低減 ・輸送効率の改善 |
たとえば、規模の経済を活用した大規模プラントの建設や、廃プラスチックを効率的に集約する仕組みが効果的です。
また、技術革新によるプロセスの簡略化やエネルギー効率の向上もコスト削減につながります。
技術革新による効率化戦略
最新のデジタル技術を活用することで、処理効率を大幅に向上させることができます。
AI・IoTを活用した自動制御システムにより、分解工程の最適化と品質管理の効率化を実現します。
▼具体的な導入事例
- 画像認識による異物の自動選別
- センサーによるリアルタイム品質管理
- ビッグデータ分析による運転条件の最適化
- 予知保全システムの導入
処理温度を下げる技術やプロセスを自動化するシステムは、運用コストの削減と生産性向上に貢献します。
さらに、AIを活用した廃棄物の分類やプロセス管理も、効率化を促進する重要な要素です。
自治体との効果的な連携方法
自治体との協力関係構築が、安定的な事業運営の鍵となります。
▼情報共有の仕組み作り
- 定期的な協議会の開催
- データ共有プラットフォームの構築
- 住民向け環境教育の共同実施
- 収集効率化のための共同研究
リサイクル専用の収集日を設けたり、市民向けの教育キャンペーンを行うことで、分別意識を高めることができるでしょう。
また、自治体が補助金を提供することで、ケミカルリサイクル事業の初期投資を軽減することも期待されます。
分別回収システムの最適化
効率的な分別回収システムの構築により、処理コストの低減と品質向上を同時に実現できます。
▼具体的な最適化方法
- 収集拠点の戦略的配置
- 人口密度に応じた配置
- アクセス性の向上
- 効率的な回収ルートの設計
- デジタル技術の活用
- QRコードによる分別支援
- スマートごみ箱の導入
- 回収状況のリアルタイム把握
- インセンティブ制度の導入
- ポイント還元システム
- 環境活動の可視化
- コミュニティ単位での目標設定
廃プラスチックの種類や状態に応じた分別技術を導入することで、リサイクル効率を大幅に向上させることができます。
さらに、地域ごとに適した回収ルートを設計し、物流コストを削減する取り組みも重要です。
まとめ
ケミカルリサイクルは、プラスチック廃棄問題の革新的な解決策として期待されています。
技術的な課題やコストの壁は存在しますが、企業や政府、地域社会が連携することで克服できる可能性があります。この技術を上手に活用することで、環境への負荷を軽減し、持続可能な社会の実現を目指しましょう。
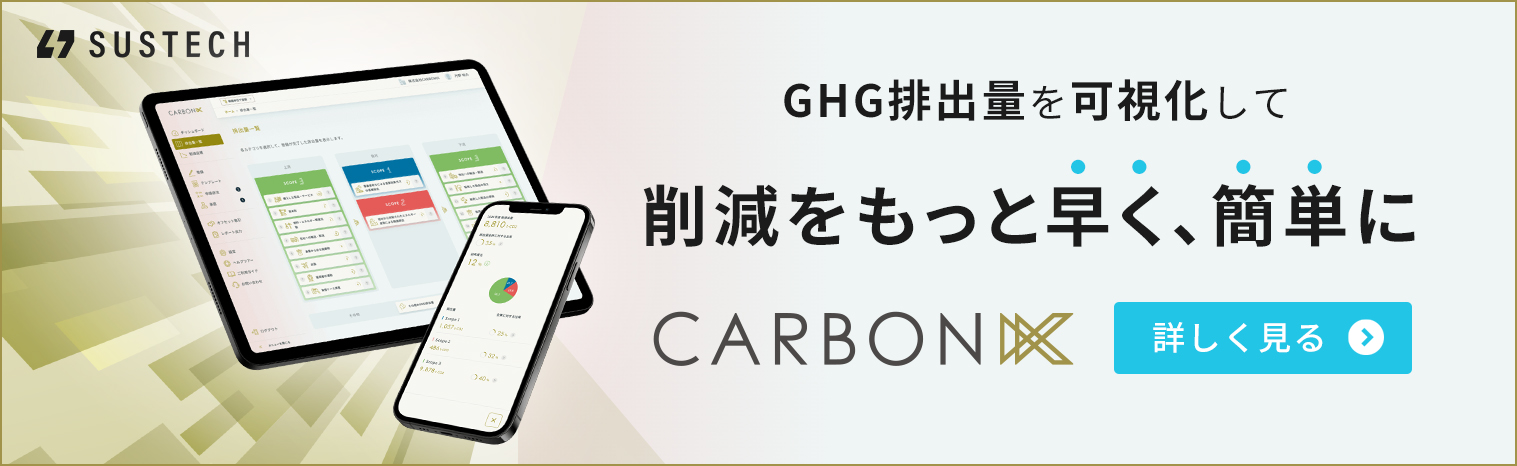
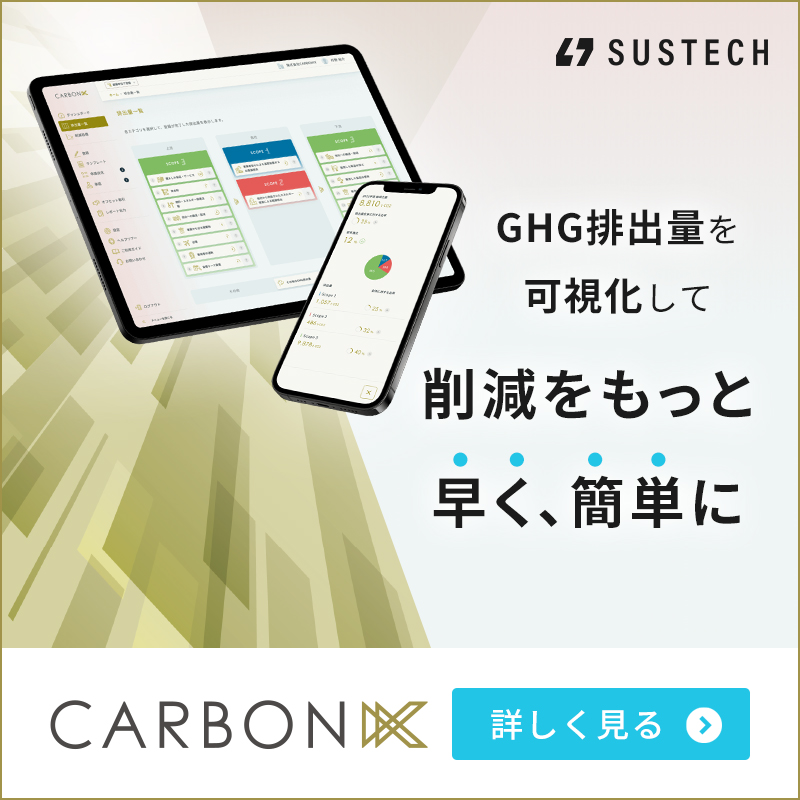